What is Product Lifecycle Management?
Product Lifecycle Management (PLM) refers to all internal processes, technologies and methods used to manage a product’s lifecycle. This cycle is separated into 4 steps: design, development, manufacture and usage. The main purpose of PLM is to ease control and to track changes of a product from its design to its withdrawal from the market.
PLM software is an application that is used to manage the data related to this whole lifecycle and to integrate the related data. PLM software can manage product-related data. It can also combine the data with ERP, MES, CAD etc. What You Will Learn: show. Web-based PLM Software Rings a Bell By Laura Carrabine October 22, 2010 MiTek Corporation designs, manufactures, and sells high performance mobile, residential, marine, and commercial audio products. The company operates three separate R&D division – mechanical, electrical, and acoustical – each focused on a different market. This not only includes its web-based PLM software solution, Devex, but the experience to understand the distinctive needs of each client, how their corporate culture distinguishes them, how this will impact which features they will need, which configurations should be made, what training will be needed, and what support maintenance should be.
Generally speaking, all product development teams use some sort of lifecycle management system. But most of the time, it is not organized by a dedicated software. Many departments are involved in product development (Marketing, R&D, Quality, etc.), who are in turn connected with suppliers and service providers, e.g. design agencies. Stakeholders often use their own templates and software, send files by e-mail, save them locally and in shared networks, etc., which leads to siloed information and data loss.
Resolving these problems is the starting point for PLM software as it centralizes all product related data and documents in a virtual vault to which every stakeholder involved in a project has access. Furthermore, it helps teams keep track of product changes and their evolution.
PLM software enable companies to centralize, share and secure information, automate processes, standardize product development methods, reduce product development time, improve communication among teams and partners, capitalize on information and tacit knowledge. Its role is to provide document organization and project information that can be modified as necessary to respond to the needs of project teams.
Web Based Plm Software Engineering
PLM software reach every department involved in a product’s lifecycle and although everyone views the product through its own lens, access to the right information at the right time is guaranteed. Once uploaded, data can be analyzed from several angles using dashboards tailored to suit various employee or business profiles. These profiles make it possible to structure information from different criteria to make it more comprehensive.
Originally, PLM was developed for the aviation and auto manufacturing industries to help manage the complexity of resources: millions of parts, sourced from thousands of suppliers.
Today, PLM is no longer limited to a specific product and addresses any company that develops products and who faces market pressures such as lowering costs, improving quality, or decreasing time to market.
PLM, by its capacity to handle complex environments, has been proven useful for Consumer Packaged Goods industries (CPG), like Food and Beverage and Cosmetics and Personal Care since the 2000s as the complexity of these sectors have grown (regulations, internationalization, market trends, etc.). The real differences between CPG industries and DMS (Discrete Manufacturing Systems) are the life span of their products and the objectives: increasing speed to market for CPG and long-term change management for DMS (unit change on plane or in a nuclear infrastructure). Moreover, CPG manufacturers face shortened product lifecycles and a great need for innovation to stay competitive. By strengthening collaboration, information sharing, and enabling the creation of a unique frame of reference, PLM solutions allow companies to capitalize on their knowledge and lay the foundation for innovation.
Is PLM right for me?
Company needs will vary based on size, business sector and level of digitalization ; but regardless of your profile, if company projects have stumbled, team communication hasn’t been optimal, regulatory requirements must be followed or costs have risen, then PLM is for you.
To ensure that the solutions offered are suited for a company’s needs, PLM software is tailored to the targeted industry. Lascom therefore has two customized solutions, one for the Cosmetics and Personal Care industry and one for the Food and Beverage industry. It is crucially important that your supplier offers a solution that meets your expectations and business requirements.
You want to discover some feedback on our PLM projects?

A PLM solution has many advantages. In addition to the benefits previously cited, it improves reliability and product quality, lowers prototyping costs and allows you to identify new development opportunities.
By improving acquired knowledge and information and capitalizing on project feedback, PLM software becomes the backbone of a project. Thanks to integrated performance indicators, project managers and general management can use the solution to help develop a strategic vision in addition to operational gains.
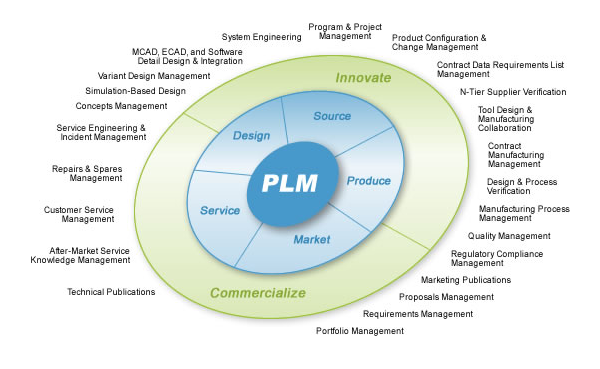
Discrete Manufacturing and Systems | Consumer Packaged Goods | |
As-design | Entity/nomenclature specific to the product design | Marketing brief and prototypes from R&D |
As-build | Entity/nomenclature originating from « As Design » adapted to product manufacturing | Identification of the ideal product/recipe from prototyping, adapted to the production system and send to the ERP |
As-maintain | Traceability via configuration management and versioning of modification operations / maintenance | Tracking evolutions thanks to elements versioning |
A modern PLM is based on:

- A data / document base enabling users to track, record every product modification and consolidate raw data. It allows data visualization (dashboard, reports, formula indicators, etc.), document management (marketing brief, specification sheets, artworks, etc.).
- A workflow engine permitting to distribute and validate data in time. Leaning on module like Nomenclature management (for DMS) or formulation management (for CPG industries), change management (versioning) and product configuration management, it enables project management and improved collaboration among stakeholders.
- A reporting engine to enhance data.
A PLM creates links among product data which enhances information by making it intelligent. It leads to impact analysis, decision support and automated generation. It allows users to see data from every point of view, or as an arborescence, and eases configuration management.
It works as a web-based interface and can be hosted in the cloud and some features are accessible on mobile devices.
PLM also goes beyond a company’s walls by inviting partners, suppliers, and customers to use the solution and while tackling growing mobility issues:
- More and more users of tablets and smartphones are accustomed to having user-friendly access to data anywhere and anytime, including data in professional contexts.
- The need to exchange data with partners and not just documents is growing in response to the internationalization of partnerships, shorter decision-making cycles and the need to consolidate data
- PLM manages all data related to product development: product description, configurations, product evolutions over time, etc.
- ERP manages sales, stocks, purchasing, billing, accounting, production.
- As for PIM (Product information Management), its role is to gather data on products to insure their efficient distribution.
There are many benefits for integrating all three solutions: smooth flow of information, data reliability, respect of deadlines, fewer errors, etc.
You can learn more in our white paper PIM -PLM: 2 complementary approaches, 1 common objective – the product information
MiTek Corporation designs, manufactures, and sells high performance mobile, residential, marine, and commercial audio products. The company operates three separate R&D division – mechanical, electrical, and acoustical – each focused on a different market. Each operated independently, using their own paper-based, ad-hoc systems to track and manage projects. But there was a problem with communications among groups, and management had no visibility into production, individually or cross-functionally.
In an attempt to fix the problem, the company decided to unify and automate processes across all three divisions. Two years ago, it evaluated several document management systems and selected Aras web-based enterprise open source PLM software. Since then, the company downloaded all the Aras community modules.
Today, two thirds of MiTek’s employees use Aras and the company houses more than 70,000 parts in its database. All R&D engineers across all divisions are trained on the software. They can create their own systems, ISO documents, workflows, and lifecycles. Quality engineers and the material planning group are self-sufficient, too.
Web Based Plm Software Developer
With Aras, MiTek now has the ability to create and maintain forms and documents, design and build their own modules, and modify any existing module to suit their needs. MiTek incorporated the use of signatures on documents, and allowed the signature to appear only after the document was approved.
Since implementing Aras, the company says it has made gains in project management and ultilization. Because the software is web-based, managers can see the status of any project, at any time. They can also optimize resources across all three R&D divisions.
Aras enabled MiTek to gain control of their processes and critical visibility into their workflow. MiTek personnel no longer spend time trying to locate documents sent off for approval. They can see the highlighted status of any
item in the workflow at any given moment.
The software is integrated into MiTek’s ERP system which helps streamline and automate the design process. Before the company used Aras, R&D teams manually completed numerous paper-based forms, and then duplicated the form for every design evaluation. They also manually entered the same information into the ERP system. Today, the company anticipates automating its engineering change process and integrating tools into Aras, and implementing help desk functionality to manage warranties, monitor problems, and track trim to repair. The company also plans to leverage the software for scrum and FEMA (failure modes and effects analysis).
Aras
www.aras.com
MiTek
www.mitekcorp.com
Web Based Plm Software Download
::Design World::
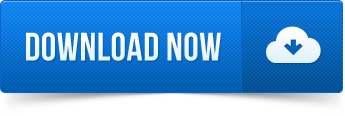